Kick-starting the circular economy: Pioneering use of Materials Passports at London’s Edenica
Designed by Fletcher Priest Architects and now under construction in the City of London, the 94,000 sq ft Edenica office development at 100 Fetter Lane is on track to set a significant sustainability precedent for UK commercial buildings.
This scheme for BauMont Real Estate Capital and YardNine is harnessing the latest design techniques to optimise operational energy efficiency and slash embodied carbon, whilst also offering class-leading user experience. As part of the development’s unique approach to cutting whole-life carbon and creating a robust platform for material circularity, Waterman’s Sustainability team is pioneering the use of Materials Passports on the project. Our multidisciplinary support for the scheme also includes building services, structural engineering and environmental specialist input, all working in close collaboration with the project team.
Materials Passports are digital data sets which describe characteristics of materials and components in products and systems, giving them value for present use, recovery and future reuse. Edenica is acting as a pilot project for their implementation and is the first scheme within the City of London to be designed as a storage bank where materials are held for future reuse.
BauMont Real Estate Capital’s Managing Director, Natalie Harrison, commented: “Our philosophy when it comes to development and refurbishment projects it to take a ‘use less, waste less’ approach. We engage sustainability specialists at the outset of our projects to ensure our desire to deliver buildings with best-in-class ESG credentials is taken into account in the early stages of design. This leads to better collaboration and promotes innovation, a good example of this being Waterman’s Material Passports initiative being delivered at Edenica, which looks beyond policy, setting a new precedent for London.”
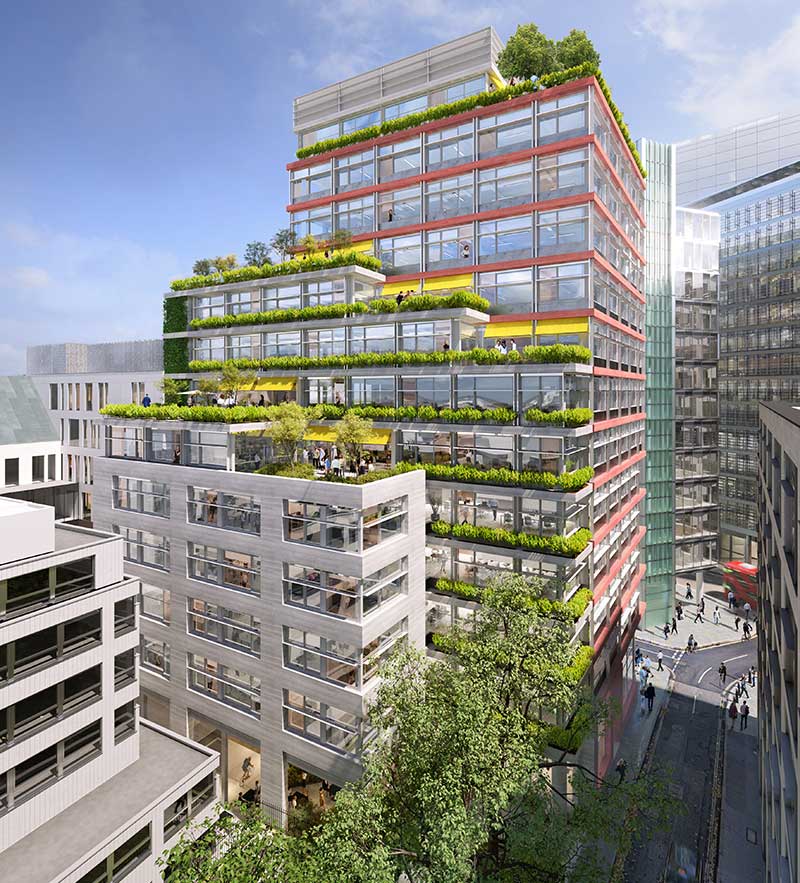
Working alongside project manager, Third London Wall, Waterman’s Sustainability team has set out the pathway for procurement to ensure the Materials Passports contain key characteristics of selected building materials held in a centralised database. This can be used to provide reports on maintenance and potential future reuse over the life of the building and beyond, maximising both material life and whole life value.
Discussing the impact of Materials Passports, YardNine’s Co-founder, Maxwell Shand, said: “Underpinned by low operational energy and an innovative approach to cutting embodied carbon, Edenica will demonstrate what can be achieved when sustainability is central to a scheme’s design ethos. I believe Waterman’s Materials Passports initiative will quickly become widely adopted as ‘best-practice’ for responsible development.”
Just as a regular passport provides personal details of an individual’s identity, Edenica’s Materials Passports represent a snapshot of the building elements’ credentials, providing records of the materials, products, and components that have been used. These records will enable the reuse of materials during the building’s operation or at the end of its life, turning the used materials into valuable resources instead of waste. Materials Passports are a relatively new initiative and are a critical step in bringing a functioning circular economy to the built environment. As a new concept in the UK construction industry, Waterman has developed a standardised framework to define the process that should be followed for their production, content or form.
The scheme’s Materials Passports will facilitate the reuse of materials in the coming years by future owners, design teams, manufacturers and contractors. For this to be most effective, the system will be calibrated to enable the constant update and maintenance of information associated with these materials throughout their life cycles.
Waterman’s Sustainability Associate, Anastasia Stella, led the development of Materials Passports at Edenica. She commented: “It is hugely important that, as construction professionals, we continually try to advance and innovate to help tackle the climate emergency. Our Materials Passports initiative shows how even the simplest of concepts can create the potential for a significant reduction in whole-life carbon and optimise re-purposing of materials in the future.”
To download your digital copy of Waterman’s Materials Passports Framework, click here.